In bulk material handling operations, conveyor systems are essential for efficient material flow. From mining and aggregates to recycling and heavy manufacturing, conveyors move raw materials and products through critical processing stages. Protecting equipment, minimizing downtime, and improving system reliability are vital for operational success.
Magnetic separators are a proven method to protect conveyor systems and downstream equipment by removing tramp ferrous metals from the material stream. These separators prevent costly damage to crushers, screens, grinders, and conveyor components while improving safety and reducing maintenance.
Types of Magnetic Separators for Conveyor Systems
Several magnetic separator designs are widely used in conveyor systems, selected based on application- specific requirements and material characteristics:
- Overhead (Suspended) Manual Clean Magnets: Positioned above conveyor belts, these magnets remove ferrous materials from the material stream as it passes below. They are effective at capturing a wide range of metal sizes, from small fragments to large structural pieces.
- Magnetic Head Pulleys: Replacing the standard head pulley, magnetic pulleys use permanent magnets to attract and remove ferrous materials as the product discharges from the conveyor. These are well-suited for continuous, automated metal separation.
- Cross-belt Separators: Mounted above the conveyor either perpendicular or parallel to the material flow, these self-cleaning systems use a continuous belt to remove ferrous contaminants from the magnet surface and discharge them separately. Cross-belt separators are ideal for high-volume applications requiring continuous operation.
Permanent Magnets vs. Electromagnets in Conveyor Applications
Choosing between permanent magnets and electromagnets is one of the most important design considerations when integrating magnetic separators into conveyor systems. Each offers specific advantages based on system capacity, material flow, and the nature of tramp metal contamination.
Permanent Magnets
Permanent magnetic separators rely on ceramic or rare-earth materials to generate a stable magnetic field without the need for external power. They deliver continuous operation with minimal maintenance requirements.
Advantages of Permanent Magnets:
- No electrical power consumption
- Low maintenance
- Consistent magnetic strength over long service life
- Cost-effective solution where power access is limited
Typical Applications:
Permanent magnets perform well in a variety of applications handling small to medium-sized tramp metal, including:
- Aggregates and sand operations
- Recycling plants removing nails, bolts, and machine parts
- Wood processing to eliminate nails and fasteners
- General material handling with shallow material layers and moderate tramp metal frequency
Electromagnets
Electromagnetic separators generate a powerful magnetic field through energized coils. Designed for high-capacity operations, electromagnets excel in demanding conditions where large volumes of material are conveyed at high speeds and where deep burden depths make tramp metal extraction more challenging.
Advantages of Electromagnets:
- Effective at capturing small, medium, and large ferrous objects
- Perform reliably in high belt speed applications
- Handle deep material burdens without loss of magnetic capture
- Suited for severe-duty environments with continuous operation
Typical Applications:
Electromagnets are widely used in operations that process high tonnage rates and need to extract a range of ferrous contaminants, including:
- Mining operations protecting crushers from tools, rebar, and structural steel
- Aggregate facilities running wide conveyors with deep burdens at high speeds
- Construction and demolition (C&D) recycling facilities removing a range of metallic contaminants
- High-capacity recycling lines capturing nails, bolts, and large scrap simultaneously
How to Select the Correct Magnet Type for Your Operation
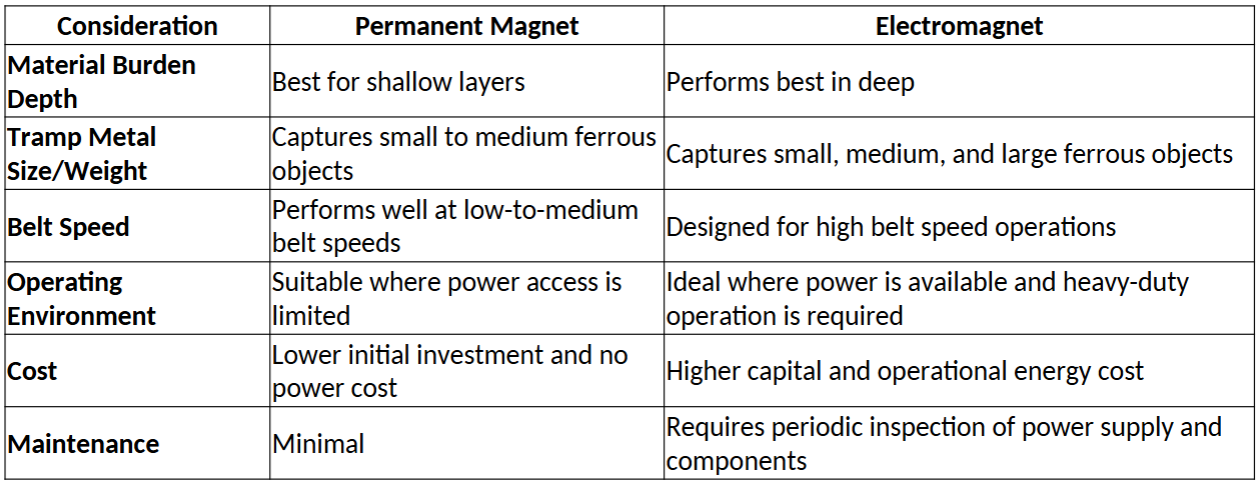
For operations with shallow material layers, moderate belt speeds, and predictable tramp metal volumes, a permanent magnet is typically sufficient. However, high-speed conveyor systems, deep burden depths, or operations facing both small and large ferrous contaminants benefit from the strength and capacity of an electromagnet.
Key Benefits of Magnetic Separators in Conveyor Systems
1. Protection of Crushers and Processing Equipment
Ferrous contaminants in material flow can cause severe damage to crushers, screens, and grinding equipment. A single piece of stray steel can crack crusher jaws, damage shafts, or compromise bearings, leading to costly downtime and repairs.
Magnetic separators remove tramp metal before it reaches processing equipment, serving as the first line of defense and significantly reducing the risk of catastrophic failures.
2. Enhanced Conveyor System Reliability
Tramp metal can tear conveyor belts, damage idlers, and misalign pulleys. Magnetic separators prevent these issues by extracting ferrous materials before they contact conveyor components. This reduces wear and tear, prevents unscheduled shutdowns, and extends system life.
3. Increased Throughput and Operational Efficiency
Self-cleaning systems like cross-belt separators and magnetic pulleys automate tramp metal removal, eliminating the need for manual intervention. This allows conveyor systems to maintain higher throughput rates, especially in high-speed operations, and reduces labor costs while improving safety.
4. Versatility Across Industries
Magnetic separators support a wide range of industries and applications, including:
- Mining and Aggregates: Protecting crushers from drill steel, bucket teeth, and rebar
- Recycling Operations: Recovering ferrous metals like nails, bolts, and structural steel
- Construction and Demolition (C&D): Extracting metal debris from concrete, asphalt, and other waste streams
- Wood Processing: Removing nails, screws, and fasteners to protect chippers and grinders
5. Reduced Equipment Wear and Maintenance Costs
Tramp metal accelerates wear on grinding mills, screens, and other high-value equipment. By removing metallic debris early, magnetic separators reduce equipment wear, extend maintenance cycles, and lower repair costs, leading to improved long-term performance.
6. Improved Workplace Safety
Sharp or heavy metallic objects in material streams pose serious safety risks. Automated magnetic separation minimizes human exposure to these hazards, supporting a safer work environment while reducing the potential for injury during manual cleanup.
Recent Comments